In today’s fast-paced world, speed to market can drive the success or failure of companies. That is certainly true for housing, retail, healthcare and, of course, industrial and manufacturing. Construction projects that support these industries represent a major investment in time and money, so delivering projects quickly and cost-effectively is paramount.
While Rockford Construction possesses experience in a variety of construction delivery methods, we have developed strong expertise in Design-Build construction, the fastest growing and most cost- and time-efficient method used to deliver projects in the U.S. In fact, of the $125 million average annual revenue generated serving industrial and manufacturing clients at Rockford, nearly 85% of our projects are completed using Design-Build.
What is the Design-Build approach and how does it differ from traditional methods?
In the traditional project delivery system (Design-Bid-Build), owners manage two separate contracts – one with the design team and the other with the construction company. Decisions are also made in a linear fashion, with less collaboration between the design and construction teams. This is not always the most advantageous method in maximizing opportunities for safety, communication, collaboration, schedule, quality and cost savings.
With Design-Build, the owner manages only one contract with Rockford as the single point of responsibility. The owner, along with the construction and design teams, collaborate from the start at conceptual design and through bidding and construction. The result is improved understanding of project goals and higher levels of communication and collaboration, creating more opportunities to provide value through cost-effective construction or alternative solutions that do not negatively impact design or schedule. Design-Build is a change in mindset from the typical linear project approach to a more fluid approach with the entire team acting as a single entity working towards common goals.
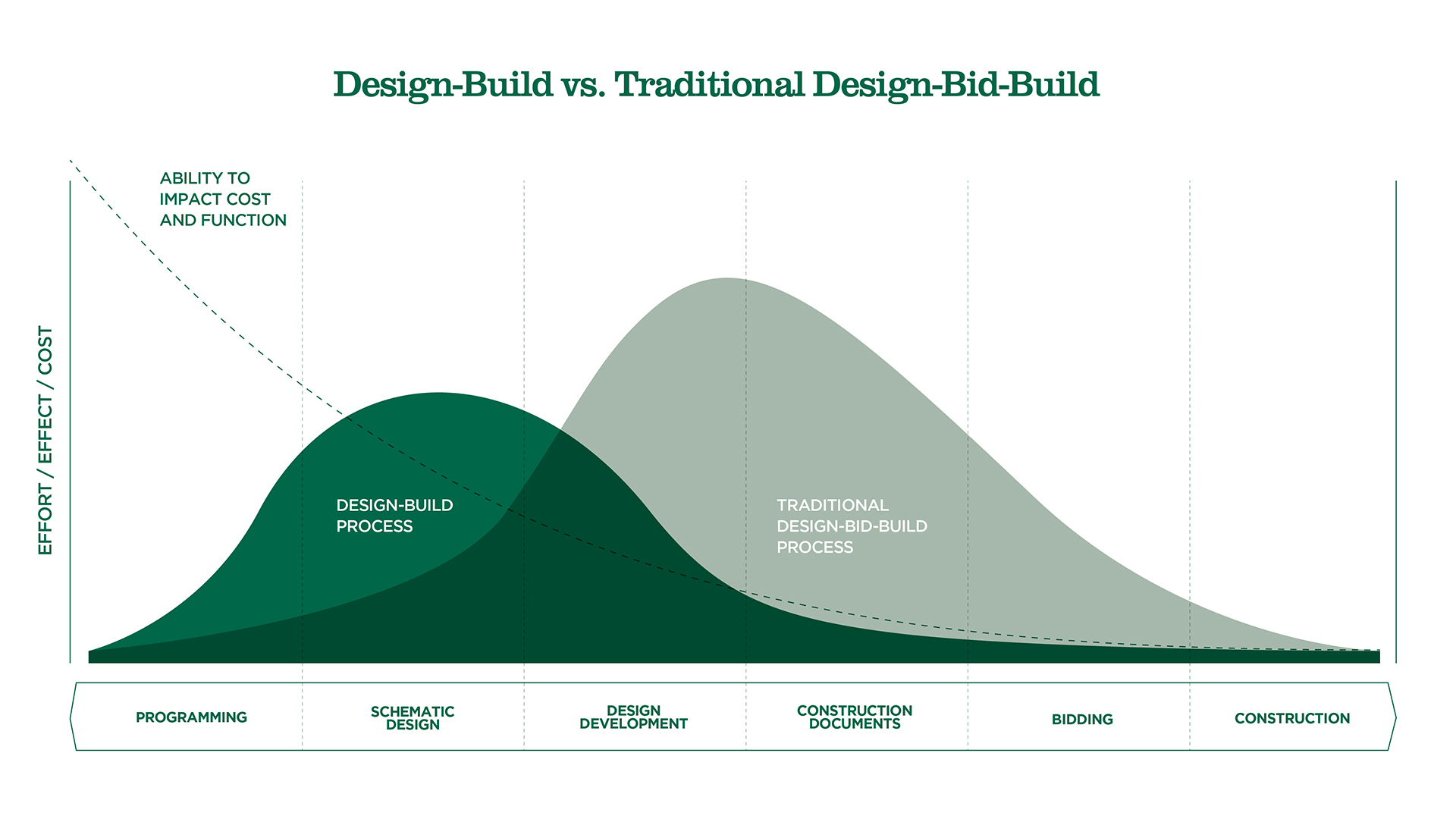
The Design-Build approach offers an improved understanding of project goals and higher levels of communication and collaboration, creating more opportunities to provide value through cost-effective construction.
“We have leveraged this approach with numerous advanced manufacturing and industrial-focused clients throughout the Midwest region,” said Josh Rewa, the Project Executive for Rockford’s industrial group.
One of Rockford’s key differentiators is its team. Jeff Taggart, DBIA, project executive, brings a certification from the Design-Build Institute of America (DBIA). This credential demonstrates and validates Rockford’s commitment to Design-Build best practices.
“Through a robust combination of education and project experience verification, this certification sets a recognized standard for Design-Build knowledge and expertise,” Rewa added.
What are the benefits of Design-Build?
According to DBIA, Design-Build is 102% faster than the traditional Design-Bid-Build approach, and results in an average savings of nearly 4% on projects – for a $5 million project, this is a savings of $200,000. For example, using the Design-Build approach on a recent project for a medical device manufacturer, our team was able to collaborate even before design started. In-depth discussions with the owner uncovered that an alternative to their specified floor coating would save hundreds of thousands of dollars without adversely affecting design or functionality. By leveraging the Design-Build approach, this client was also able to begin manufacturing sooner by utilizing a phased execution plan, placing priorities on areas of production – one of the many benefits to using a Design-Build approach.
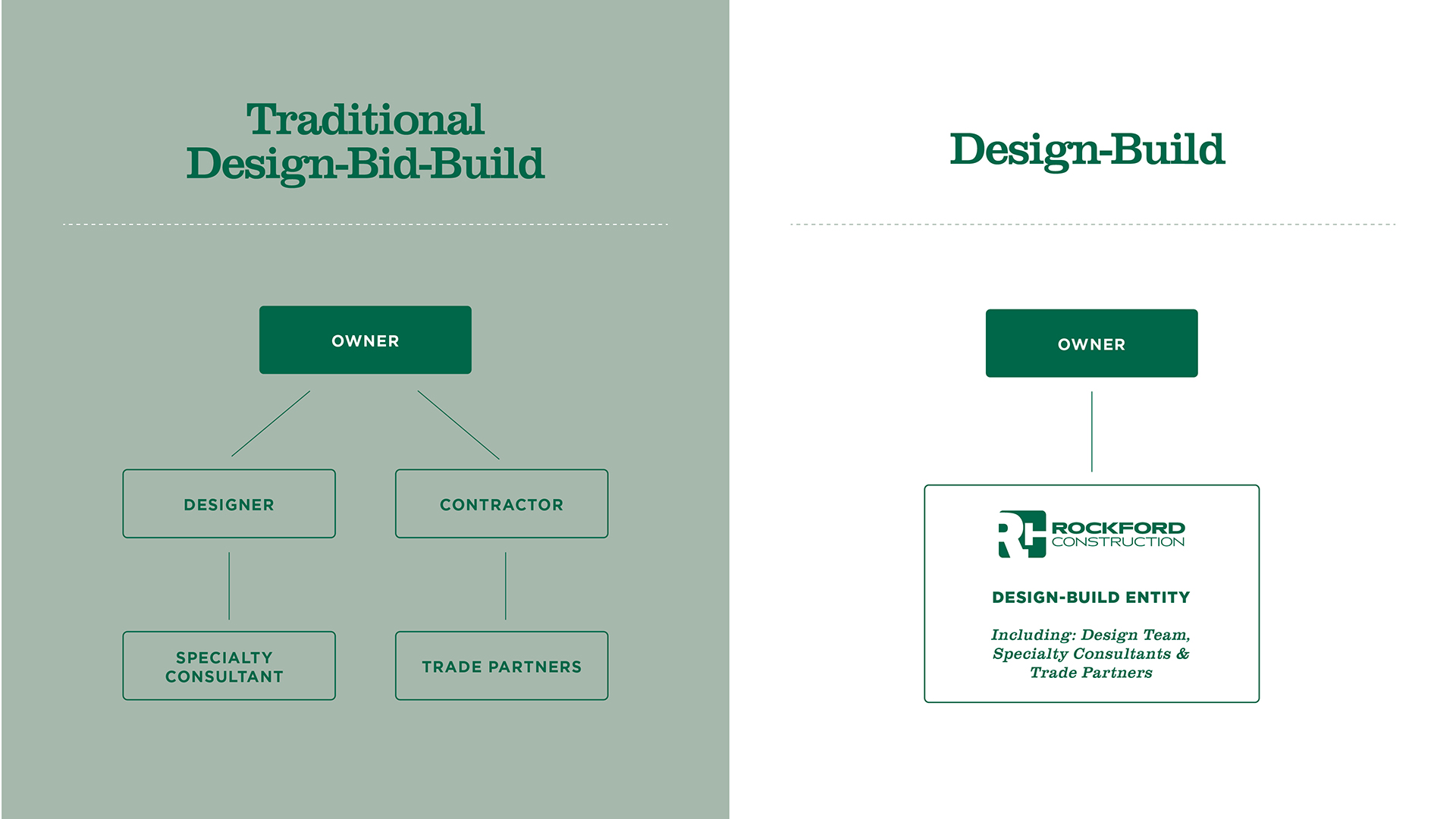
According to DBIA, Design-Build is 102% faster than the traditional Design-Bid-Build approach, and results in an average savings of nearly 4% on projects.
Additionally, on a recent project for an aerospace manufacturer, our early involvement in the design development phase allowed for clear communication surrounding redundancy of the mechanical and plumbing systems. This avoided redesign, aligned the necessary scope and project goals, and significantly impacted the project by reducing the overall budget and schedule.